Fuel Brake testing of car fuel and brake parts/congregations is testing. Regardless of whether it is more up to date discharge and security determinations or more tightly OEM details, ATC has broad learning and involvement in the car business.
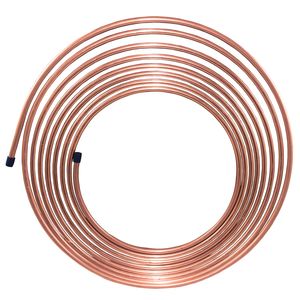
We’ve built up some of these determinations for Fuel Brake and vapor parts. ATC Brake System Leak Testing items surpass the necessities of basic SAE and OEM prerequisites, performed at high weight. Our choking tests go along to US-DOT prerequisites.
Nicopp Brake Line Review
A vehicle’s stopping mechanism is as significant to a vehicle’s execution as its motor and drive prepare. The tubing helping pressurized air or liquid through the framework is theĀ Nicopp Brake Line indispensable connection between ace chamber and slave barrels at the wheels.
Slowing mechanism tubing is helpless against the weights of air or liquid coursing through it, to erosion from street mud and salt, and to harm of any defensive coatings on its surfaces from stone pecking where it is uncovered under the case.
Before 1930, copper and metal, having amazing inborn weight containing and hostile to consumption qualities, were the materials of decision for brake tubing. By post World War II, car industry large scale manufacturing financial matters directed reception of an ease type of twofold wrapped, heater brazed steel tubing that is still being used today around the world.
Having amazing, starting weight bearing attributes, steel tubing is, notwithstanding, defenseless to consumption. To impede its characteristic corrodibility, coatings of different materials, e.g., zinc-rich paint, terne (a lead/tin amalgam) and epoxy, have been connected to steel tubing outsides.
Be that as it may, no covering has turned out to be absolutely impenetrable to setting, scraping and chipping because of defective produce, indiscreet establishment and introduction to unfriendly ecological conditions like free rock. An entered covering permits the consumption procedure to start.
An inalienably consumption safe tubing material is the best way to guarantee proceeding with viable erosion protection.
Copper-nickel composite C70600, a combination of 90% copper and 10% nickel, is intrinsically erosion impervious to street salt, and its utilization as brake tubing is expanding in light of: 1) Changing future for car vehicles; 2) Worldwide administration encounter information on brake tubing wear; and 3) Increasing expense of consumption hindering coatings for steel brake tubing.
Highlights and Benefits
Unit incorporates: 3/16″ x 25′ NiCopp Coil, 1/4″ x 25″ NiCopp Coil, 3/16″ Fitting Assortment, and 1/4″ Fitting Assortment for working with any household or import 3/16″ or 1/4″ brake line framework, Brake line substitution guideline sheet. NiCopp is a nickel-copper composite brake tubing that meets SAE Standard J1047 and ISO 4038; meeting all global and U.S. necessities for brake tubing.
This amalgam is around 9.2% nickel, 1.4% iron, 0.8% manganese, and 88.6% copper.Under the UNS framework, this combination is assigned as UNS C70600. NiCopp along these lines has the quality and auxiliary honesty of steel lines yet with the additional advantage of being significantly more erosion safe.
Nicopp Brake Line is likewise less demanding to curve and frame than steel tubing. Nickel-copper, regularly alluded to as ’90-10 copper’, has been utilized on a few European vehicle slowing mechanisms since the 1970’s, including: Volvo, Audi, Porsche, and Aston Martin.